2. I processi di filtrazione e la classificazione delle membrane (1 di 2)

La filtrazione su membrana consiste nella separazione di due o più componenti all’interno di una corrente liquida in base alla differenza tra la dimensione dei pori del mezzo filtrante e la dimensione dei componenti da rimuovere: il risultato consiste nell’ottenimento di due flussi in uscita (permeato e concentrato) da un flusso in ingresso (alimento). Questo è possibile mediante impiego di una forza motrice che, in questo caso, è rappresentata da un gradiente di pressione. A seguito dell’accumulo dei componenti rimossi sulla superficie ed all’interno della membrana stessa, si assiste al graduale incremento del gradiente di pressione richiesto. Questo fenomeno, detto sporcamento (o fouling), è mitigabile mediante diversi accorgimenti che saranno analizzati all’interno di un successivo post.
Di seguito, una breve panoramica delle principali classificazioni delle membrane utilizzate in applicazioni MBR.
In base alla modalità di funzionamento, ovvero alla direzione dei flussi di alimento, permeato e concentrato, si distinguono membrane operanti in:
Dead-end (o full-flow), qualora il flusso di alimento sia perpendicolare alla membrana e non vi sia quindi flusso continuo di concentrato. Questa soluzione consente minori consumi energetici a prezzo di un più rapido incremento della resistenza alla filtrazione (e, quindi, di interventi di pulizia più frequenti) ed è, pertanto, impiegata in caso di acque di alimento con basso contenuto di solidi sospesi e di sostanze in grado di sporcare le membrane (e.g. filtrazione di acque superficiali);
Crossflow (o tangenziale), qualora il flusso di alimento sia parallelo alla membrana e perpendicolare al flusso di permeato ed il concentrato fluisca continuamente dall’uscita del modulo di membrane. Questa soluzione consente di limitare l’incremento di resistenza alla filtrazione nel tempo (grazie all’abrasione esercitata dal flusso di alimento sulla superficie delle membrane) a prezzo di maggiori consumi energetici (dovuti alla necessità di ricircolare il concentrato o di scuotere le membrane con aria) ed è, pertanto, impiegata in caso di acque di alimento con elevato contenuto di solidi sospesi e di sostanze in grado di sporcare le membrane (e.g. applicazioni MBR).
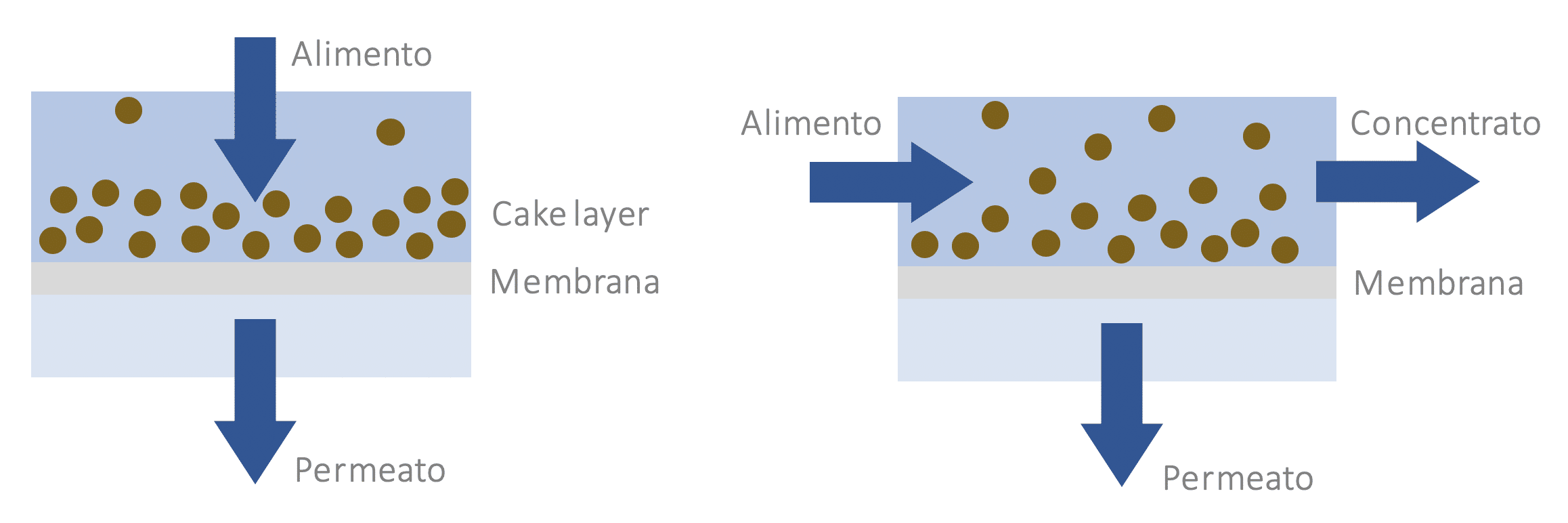
Figura 3. Schema concettuale della filtrazione dead-end (sinistra) e crossflow (destra).
In base alla direzione del flusso liquido, si distinguono membrane operanti:
Out-to-in, qualora l’alimento attraversi la membrana dall’esterno ed il permeato venga raccolto all’interno della membrana stessa. In questo caso, in campo MBR, si applica una pressione negativa (ovvero, un certo grado di vuoto), solitamente pari a 0.05 ÷ 0.5 bar, e si opera ad un flusso costante (facendo, quindi, variare la TMP): questo è tipico delle membrane piane ed a fibra cava;
In-to-out, qualora l’alimento scorra all’interno delle membrane ed il permeato venga raccolto all’esterno della membrana stessa. In questo caso, in campo MBR, si applica una pressione positiva (ovvero, una certa sovra-pressione), solitamente pari a 2 ÷ 7 bar, e si opera a TMP costante (facendo, quindi, variare il flusso): questo è tipico delle membrane tubolari.
Figura 4. Schema concettuale della filtrazione out-to-in (sinistra) ed in-to-out (destra).
In base al materiale, si distinguono membrane:
Polimeriche. In campo MBR, si prediligono membrane organiche di tipo sintetico, realizzate in PVDF o PES. In particolare, questi materiali sono modificati con processi proprietari al fine di aumentare l’idrofilicità della membrana e migliorare, quindi, le performance di filtrazione;
Ceramiche. In campo MBR, si prediligono membrane ceramiche in ossido di alluminio (Al2O3) o carburo di silicio (SiC). Rispetto alle membrane polimeriche, le membrane ceramiche sono caratterizzate da maggior resistenza meccanica, termica e chimica, maggiori flussi e minori frequenze di lavaggio chimico (grazie al minor potenziale zeta), possibilità di controlavaggio con flussi superiori (grazie alla maggior resistenza meccanica), possibilità di lavaggio chimico con modalità più “drastiche” (grazie alla maggior resistenza chimica) e da prezzi sensibilmente superiori (a causa del processo produttivo, che richiede elevati input energetici).
Tabella 1. Materiali delle membrane utilizzate in applicazioni MBR.
Materiale |
PVDF |
PES |
Al2O3 |
SiC |
Idrofilia |
Bassa |
Media |
Medio-alta |
Elevata |
Range di temperatura 1 |
5-40°C |
5-40°C |
5-40°C (90°C) |
5-40°C (90°C) |
Range di pH 2 |
(1) 2-10,5 (12) |
1-13 |
0-14 |
0-14 |
Tolleranza al cloro |
Elevata (1.000.000-2.000.000 ppm Cl2 x h) |
Media (250.000-500.000 ppm Cl2 x h) |
Ininfluente |
Ininfluente |
1 Il limite superiore è dovuto ai materiali di costruzione del blocco o modulo.
2 I limiti sono dovuti agli additivi utilizzati per modificare il polimero di base e/o ai materiali di costruzione del blocco o modulo.
In campo MBR, le membrane ceramiche sono solitamente limitate al trattamento di reflui altamente concentrati, al trattamento di reflui con elevato potenziale di sporcamento (e.g. per presenza di elevate concentrazioni di grassi ed oli) e/o ad elevate temperature di processo (i.e. reattori MBR anaerobici operanti in campo termofilo). Grazie all’elevata resistenza meccanica e chimica, le membrane ceramiche possono risultare attrattive anche in caso di impianti MBR civili decentralizzati.
In base alla geometria dei moduli, si distinguono:
Membrane a fibra cava (Hollow Fiber, HF), realizzate depositando la soluzione polimerica all’esterno di un cilindro in carta porosa (fibre non supportate) o tessuto (fibre supportate), dove la seconda alternativa è la più comune nelle applicazioni MBR in virtù della maggiore resistenza meccanica. Il diametro esterno delle membrane a fibra cava è inferiore a 3 mm. Più membrane a fibra cava sono installate all’interno di un modulo mediante incollaggio con resina epossidica e più moduli sono assemblati all’interno di un frame ad avere le cassette. Critica è la resistenza agli estremi di ogni fibra cava e critico è l’impiego di soluzioni per evitare l’accumulo di fango/detriti nelle zone ove la turbolenza è minore;
Membrane piane (Flat Sheet, FS), realizzate adagiando la membrana polimerica ai due lati di uno strato di non-tessuto (“permeate spacer”) che previene il collasso della membrana stessa e facilita il collettamento del permeato verso i relativi punti di estrazione. In alternativa, le membrane piane possono essere realizzate in ceramica mediante sinterizzazione del supporto, successivo rivestimento con lo strato selettivo e sinterizzazione finale del composto. Più membrane piane sono installate all’interno di blocchi che vengono poi assemblati all’interno di un frame ad avere i moduli. In caso di membrane polimeriche, critica è la resistenza dei lati di ogni membrana piana (ove le membrane sono saldate tra loro) e, sia per membrane polimeriche che ceramiche, critico è il distanziamento tra due membrane piane successive;
Membrane tubolari (Multi-Tubular, MT), realizzate depositando la soluzione polimerica all’interno di un cilindro in carta porosa od in materiale plastico o con un processo produttivo analogo a quello delle membrane FS ceramiche. Il diametro interno delle membrane è pari o superiore a 4 mm. Più tubi vengono assemblati all’interno di un modulo mediante incollaggio con resina epossidica od analoghe soluzioni di ancoraggio. Critica è la resistenza dei punti di ancoraggio delle membrane al modulo e critica è la necessità di evitare l’occlusione dei tubi di flusso.
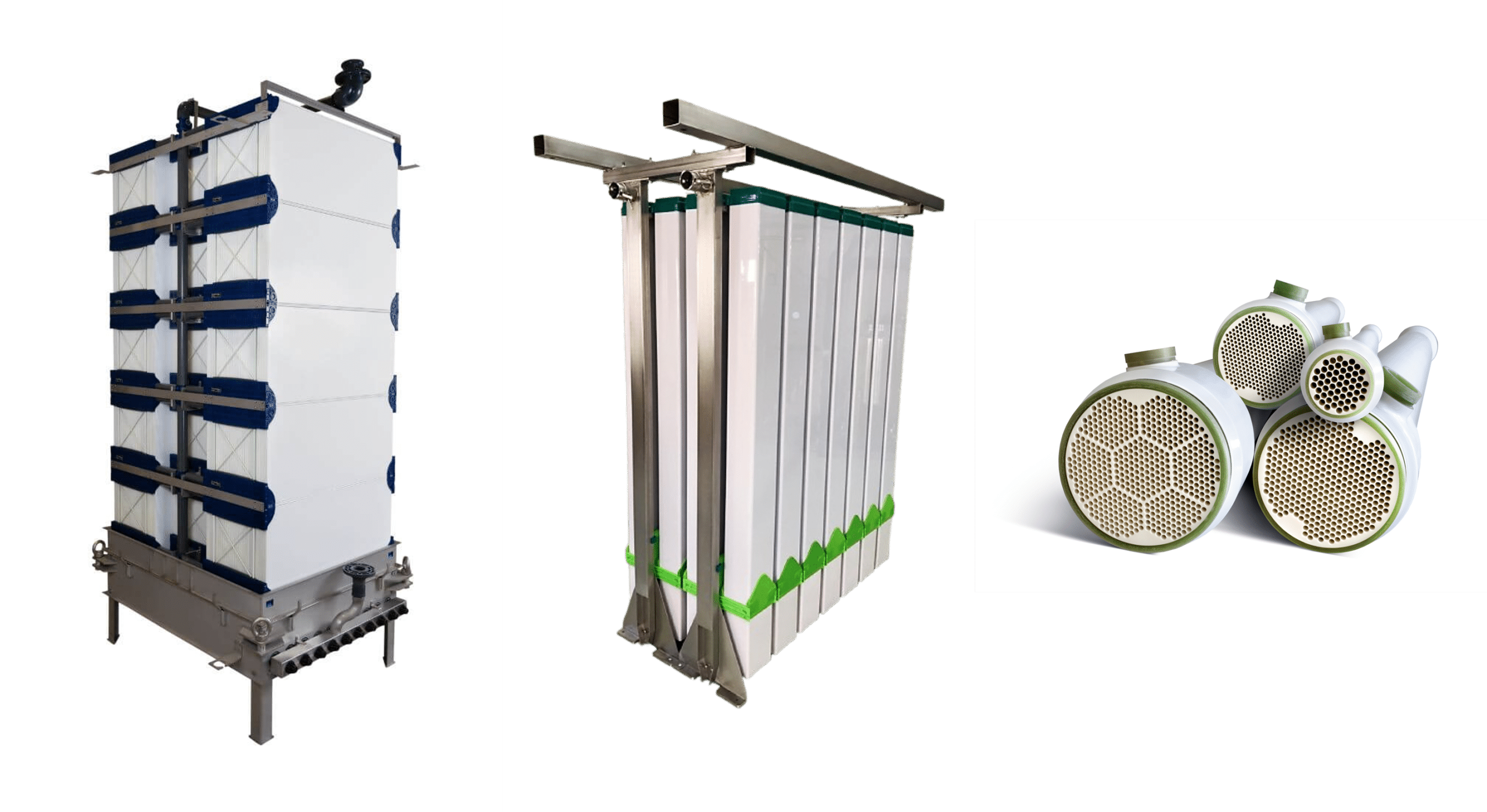
Figura 5. Esempi di membrane a fibra cava (sinistra), piana (centro) e tubolare (destra).